The Tapestry Company, (Brose Patrick Scotland) Ltd.. 1970 - 1974
In 1970, Gerald Laing started a tapestry company. "This was not because I had any particular passion for the medium. Contemporary tapestries have a problem because they are positioned somewhere between art and craft, and are far more expensive to make than paintings.But it was for this reason that I chose them.
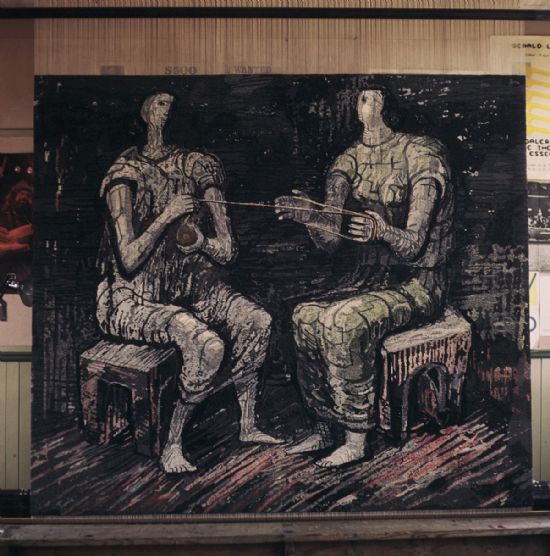
HENRY MOORE - Women Winding Wool. 8 feet x 7 feet. Woven by the Tapestry Company, Brose Patrick (Scotland) Ltd., in 1972. The source was an early drawing provided by Henry Moore.
They satisfied three crucial criteria – 1. They used a local material (wool) 2. They required no fuel or machinery 3. And above all, their production is labour intensive. These qualities could provide intelligent work in an area of chronic underemployment. The project was completely opposite in character to the oil industry. I found a tremendously skilled and generous supporter in Archie Brennan, who at that time was in charge of the Edinburgh Tapestry Company (a.k.a. The Dovecot), at which he had been originally apprenticed as a boy. He came and trained my weavers and would accept no remuneration for so doing.
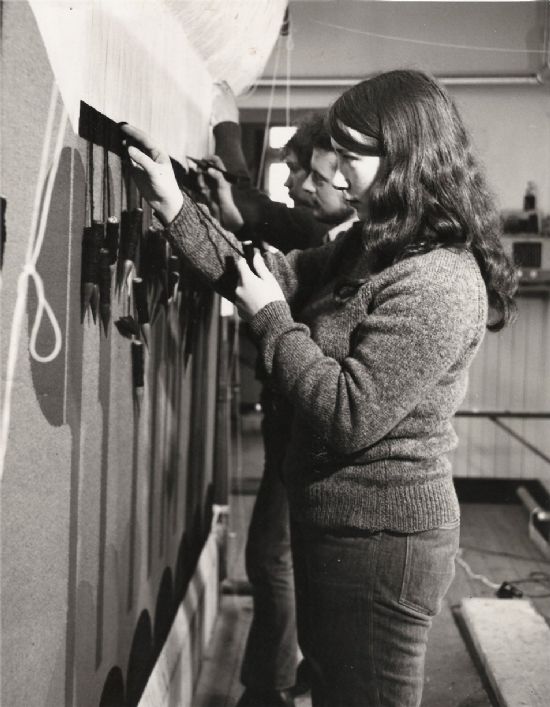
I advertised and found four local youths and one girl who were prepared to become weavers. For aesthetic, not practical, reasons, I rented a small ex-schoolhouse in the hills at Loch Ussie, about six miles from Kinkell. Everything about my new small industry was to be idealistic. At first we even dyed our own wool colours, but worries about colour fast quality soon caused me to obtain wool from the many tweed mills which then existed. It was surprising to me to see that very bright strong colours are used in the production of that tweed cloth which invariably seems to end up as greenie brown or brownie green. The Highlands and Islands Development Board were finally cajoled into providing a small grant to help me to get started . The weavers became extremely expert.
At first, I designed many of the tapestries myself, but soon the cost of manufacture made itself felt. Even after the weavers became fully competent, the finished product was expensive. Then, suddenly, we were approached by the art dealer Thomas Gibson, who had persuaded Henry Moore to allow certain of his early drawings to be made into tapestries. Moore’s ultimate selling price could easily absorb the cost of weaving in a way beyond the power of younger and less successful artists, some of whom I had persuaded to make tapestries.
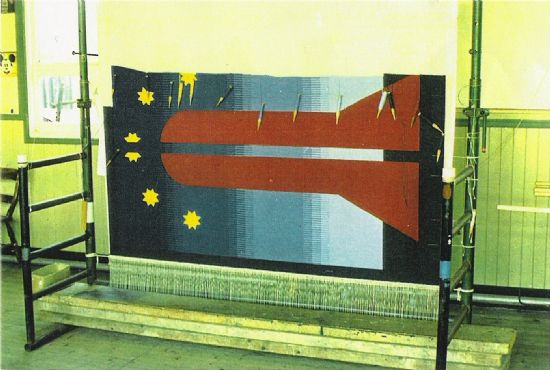
Thereafter we had the incredible paradox of five Highland teenagers, who had never looked at art before, weaving enormous tapestries, each based on a quite small and complicated drawing and a primitive black and white full scale photostat of that drawing, in which red, for example, appeared as black, and yellow did not show up at all. My weavers usually made all of the necessary editorial decisions regarding inclusion, omission and interpretation, transposing wax spots, ink and paint into wool in a modular, virtually digital, framework of warp and weft. I would interrupt my studio work in order to visit the workshop once a day, and seldom had to make any major alterations to their translation of the images from one medium to the other. It was remarkable how well they carried out this task.
On completion, each tapestry would be checked by Henry Moore; then the dealers would take over and sell these tapestries for large sums. And so this went on for four years, from 1970 until 1974. We achieved full and happy employment under excellent working conditions, for a wage commensurate with that attainable at that time in any other work – except in the North Sea Oil industry.
And that was the problem; the huge growing pains of speedy development and the change such activity wrought, welcome or not, on the existing established systems. Eventually my weavers caught the bug too. They could earn four or five times what I could pay them if they worked for oil. And who could blame them? So after four years they left, and, with a sense of relief, I closed down the workshop.
Later, I was told that in terms of sheer cost per head it was the most successful project the HIDB had ever supported. It provided employment in idyllic conditions; it produced beautiful objects; and it did no harm."